Nordex zählt zu den weltweit größten Produzenten von Windkraftanlagen. Bei der Versicherung der Produktionsstätten vertraut das Unternehmen aus Rostock schon seit mehr als zehn Jahren auf die Allianz. Ein Werksbesuch in den Hallen der Turbinenfertigung
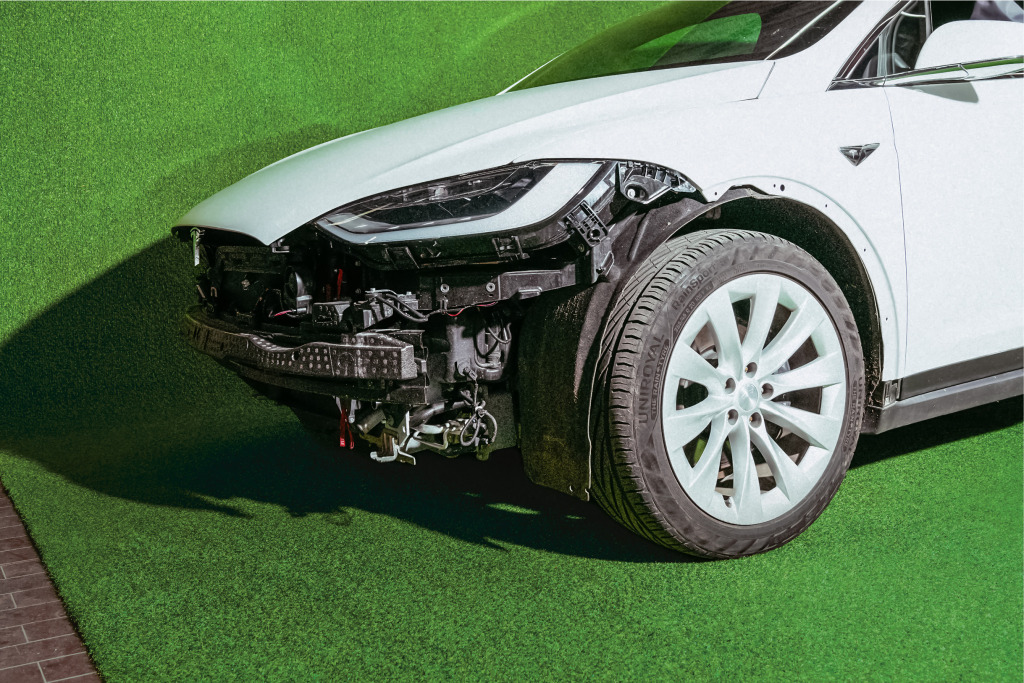
Klicken Sie sich durch die Bildergalerie: Die Personen hinter den Windrädern
Auch bei der Antriebsmontage gibt es sie: Minuten der Romantik. Dann schlägt sogar das Herz eines noch so sachlichen Konstrukteurs ein kleines bisschen höher. Denn wenn sich die Karosserie und der Motor auf dem Fließband vereinen, erreicht die Fertigung eines Fahrzeugs ihren Höhepunkt. »Hochzeit« nennen Autobauer diese Verkupplung der wichtigsten Maschinenteile. Auch bei Nordex in Rostock fiebert Manufacturing Engineer Till Sachse dieser Zeremonie entgegen. »Das erfordert immer wieder besonderes Fingerspitzengefühl«, erklärt der 31-jährige Ingenieur.
In den Werkshallen des Windkraftanlagen-Herstellers »heiraten« der Maschinenträger und der Generatorträger – die beiden bilden das Herzstück eines sogenannten Maschinenhauses. Diese 70 Tonnen schweren, 4 Meter hohen und 13 Meter langen, mit Glasfaserkunststoff verkleideten Kraftwerke werden im Rostocker Produktionsstandort von Nordex zusammengebaut und auf den Transport vorbereitet. Das Maschinenhaus sorgt dann auf dem Turm der Windkraftanlage in erster Linie dafür, dass die Rotorblätter immer passend im Wind stehen und ihre Drehung in Strom umgewandelt wird.
Um den Maschinen- und Generatorträger zu verbinden, braucht es kein Fließband, sondern die kräftigen Hände von Kranführer Alexander Brandhorst. Konzentriert packt er vier schwere Eisenketten, die an einem Kran unter der Hallendecke befestigt sind. Eine nach der anderen hakt er in den Generatorträger ein. Dann hängt er sich seine Fernbedienung um den Hals und lässt das neun Tonnen schwere und rund vier Meter hohe Bauteil in die Luft steigen und steuert es über den Gang des Werks auf die andere Seite der Produktionsstationen. Dort wartet der Maschinenträger schon gut fixiert auf der Basis des Maschinenhauses. Langsam wird das Paar zusammengeführt und gegeneinander verschraubt. Millimeter für Millimeter justiert Kranführer Brandhorst nach, damit die Zentrierdorne in die vorgefertigten Löcher des Maschinenträgers passen. Ein kleiner »Wetten-dass«-Moment, wo einst Baggerfahrkünstler mit der Schaufel den Nippel durch die Lasche zogen.
Ferngesteuertes Hightech statt Schienen
Auch wenn der Routinier das mehrmals täglich macht, sagt er: »N’ bisschen kribbelig ist das schon. Aber uns ist noch nie ein Brautpaar vom Tisch gefallen.« Mit »Tisch« meint er die gelben Stahlplatten auf acht Füßen. Auf denen wandern die Maschinenhäuser von Station zu Station. Und zwar mittels ferngesteuerter Hightech-Apparate. Wie eckige Mega-Saugroboter fahren diese unter die Tische, hieven sie samt Gondel hoch und transportieren die halb fertigen Baugruppen weiter. Die Innovation hat die starre Fließbandfertigung auf Schienen überflüssig gemacht. Heute kann man so die Halle des ehemaligen Dieselmotorenwerks viel flexibler und effektiver nutzen.
Ebenso den Geräuschpegel hat man durch den Verzicht auf die Schienen in der 9500 Quadratmeter großen Halle gesenkt – selbst wenn manchmal der Schlagschrauber schrillt, der Gabelstapler über den Flur surrt oder ein Arbeiter seinem Kollegen etwas zuruft. Auch unter den Mechaniker:innen herrscht konzentriertes Werkeln. Kein hektisches Schrauben. Kein nervöses Justieren. Man merkt nicht, dass hier alle einen sportlichen Takt zu erfüllen haben. 17 Stationen durchläuft ein Maschinenhaus, bis sämtliche Teile montiert sind. Für jede Station haben die Mitarbeitenden vier Stunden Zeit. Im Wesentlichen werden vier Hauptkomponenten verbunden: Stahlunterbau, Generator, ein Schalthaus für die Elektrik – und später im Windpark der Triebstrang. Gearbeitet wird in Schichten, sodass nach sieben Tagen ein Produkt einsatzbereit ist. Und weil parallel an mehreren Maschinenhäusern geschraubt wird, können pro Woche bis zu 20 Stück das Werk verlassen.
Natürlich ergeben sich dabei auch Herausforderungen, wie Sachse es formuliert. Besonders wenn es zu Verzögerungen kommt – etwa durch fehlerhafte Materialien oder verspätete Anlieferung. »Einmal wurde eine Stahlkonstruktion geliefert, die falsch konserviert worden ist«, erinnert er sich. Das Problem: verminderte Reibung. »Wir mussten alle Gewinde und Bohrungen erst mal gründlich säubern.« Ein Prozess, der eine Stunde dauerte – so lange stand die Linie still. Erst danach konnte die Produktion weiterlaufen. Solche Verzögerungen passieren jedoch selten. »Wir rechnen mit einer Linienverfügbarkeit von 90 Prozent«, erklärt Sachse.
Innenleben mit rund 9600 Einzelteilen
Eine in der Produktion notwendige Zahl, aber auch eine erstaunliche. Immerhin werden in einem Maschinenhaus mehr als 1200 Komponenten verbaut – die wiederum aus insgesamt rund 9600 Einzelteilen bestehen und aus der ganzen Welt kommen. Zum Beispiel Stahlunterbauten aus China. Oder Generatoren aus Deutschland. Glasfaserkunststoff aus Litauen. Transformatoren aus Österreich. Drehkränze aus Mexiko. Schrumpfscheiben aus Italien. Hydrauliksysteme aus der Türkei. Oder Getriebe made in Sachsen. Triebstränge und Schaltschränke baut Nordex selbst.
Die hiesige Montage ist mittlerweile in der internationalen Branche etwas ganz Besonderes. Auch Nordex fertigt zum Teil im Ausland, um kostengünstig zu produzieren und die Transportwege in internationale Märkte zu verkürzen. Das Unternehmen hat beispielsweise Produktionsstandorte in Brasilien, Mexiko, Spanien und Indien, setzt aber ebenso auf den Standort Deutschland. Erst 2023 hat die Geschäftsführung rund zwei Millionen Euro in die Modernisierung der heimischen Fertigung investiert. Damit man beim Bau der immer größeren und schwereren Turbinen-Generationen global mithalten kann. Dazu kommt, dass 60 Prozent der Aufträge aus Europa stammen und so kürzere und bessere Transportwege für die Riesenbauteile genutzt werden können.
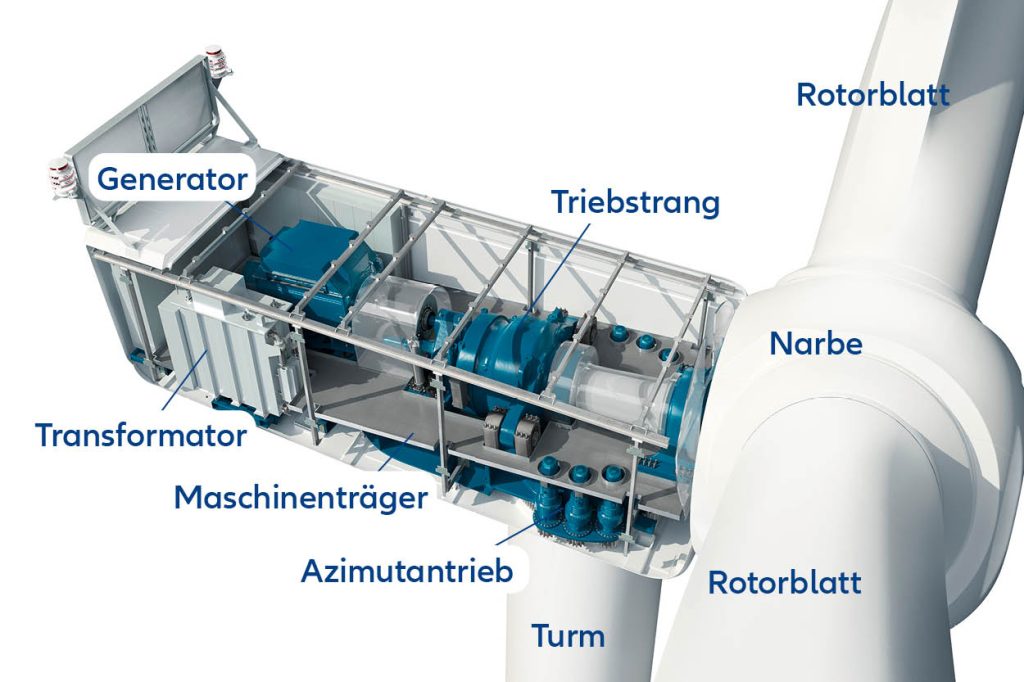
Die ambitionierten Ziele der Bundesregierung
Zudem glaube man an den Ausbau von Windkraft hierzulande. »Auch wenn – oder ich sollte besser sagen: gerade weil – die Bundesregierung immer noch mit ihren Plänen hinterherhinkt«, meint Sachse. Das große Ziel des sogenannten Erneuerbare-Energien-Gesetzes steht nach wie vor: Bis zum Jahr 2030 sollen mindestens 80 Prozent des Stroms aus erneuerbaren Quellen stammen. Allein die Leistung durch Windkraftanlagen an Land muss sich bis dahin mit 115 Gigawatt fast verdoppeln. Ende 2040 sollen es sogar 160 Gigawatt sein. Zwei Prozent der Landesfläche Deutschlands wären dafür erforderlich. Aktuell beträgt die installierte Leistung der 28 667 Onshore-Windräder der Republik insgesamt nur 61 Gigawatt. Deswegen montieren im Stammsitz heute mehr als 770 Mitarbeitende die Hälfte aller Nordex-Maschinenhäuser. Das sind rund 700 Stück pro Jahr, was einer Leistung von etwa 3,4 Gigawatt entspricht.
Die Investition in die heimische Zukunft zeigt sich auch in den 50 Azubis, die Nordex aktuell ausbildet. Eine davon ist Sabrina Rietz. Sie absolviert gerade ihr zweites Ausbildungsjahr als Mechatronikerin in der Nabenfertigung. »Die Arbeit macht mir Megaspaß«, sagt die 28-Jährige. Besonders gefalle ihr die Abwechslung. Sie darf in alle Bereiche reinschnuppern, egal ob Hydraulik, Pneumatik, Elektrotechnik oder Mechanik. »Ich freue mich auch schon total darauf, wenn ich für die Reparatur direkt aufs Windrad darf«, erzählt die gebürtige Rostockerin. Denn neben der Fertigung bietet Nordex seinen Kunden auch die Instandhaltung seiner Windparks. Ihr Faible fürs Handwerk hat Rietz durch ihre Familie entdeckt. Ihre Eltern sind Metzger, ihre Oma war Schlosserin. Aber die Entscheidung für Nordex habe sie vor allem wegen der Nachhaltigkeit getroffen. »Ich habe eine kleine Tochter«, erklärt Rietz, »ich möchte, dass sie eine lebenswerte Zukunft hat.«
»Mich überzeugt bei Nordex einfach die Sinnhaftigkeit der erneuerbaren Energieerzeugung«
Manufacturing Engineer Till Sachse
Die Turbinenleistung hat sich seit 1999 versechsfacht
Auch Sachse überzeugt die nachhaltige Arbeit. »Als Ingenieur habe ich in der Industrie eigentlich überall gute Arbeitschancen. Aber mich überzeugt bei Nordex einfach die Sinnhaftigkeit der erneuerbaren Energieerzeugung«, sagt der studierte Maschinenbauer. »Und natürlich die rasante Entwicklung zu immer leistungsstärkeren Turbinen«, ergänzt er. Allein bei Nordex hat sich die technische Entwicklung seit 1999 enorm gesteigert. Hat man damals noch Turbinen mit rund 1 Megawatt Leistung gebaut, verlassen heute mit der neuen Delta-4000-Generation Exemplare mit bis zu 6 Megawatt das Werk.
Gerade wird so ein fertiges Prachtstück bei Station 17 von vier Mitarbeitern in einer Plastikplane verpackt. Sie versiegeln das Loch an der Front des Maschinenhauses. Dort, wo später auf dem Windradturm die Nabe mit den Rotorblättern montiert wird. Das Hallentor öffnet sich, und ein Schwerlasttransporter fährt rückwärts rein. Kranführer Brandhorst lässt das Maschinenhaus wieder in die Höhe steigen und sanft auf die Ladefläche des Lkw absinken. Mechaniker fixieren es mit schweren Eisenketten. Danach rollt der Laster Richtung Straße.
Text Sonja Hoogendoorn
Fotos Maximilian Mann